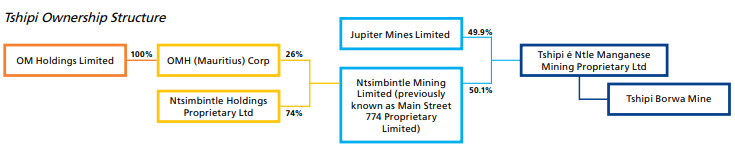
OM Holdings Ltd. has an effective 13% stake in the tier-1 Tshipi in South Africa. OMH’s stake in Tshipi is via its 26% strategic partnership with Ntsimbintle Holdings Proprietary, the majority 50.1% owner of Tshipi. The remaining 49.9% share is owned by Jupiter Mines, an Australian-listed mining company.
Jupiter Mines Limited has an interest 49.9% share in Tshipi é Ntle Manganese Mining (Proprietary) Limited, which operates the Tshipi Borwa Manganese mine in South Africa.
Contractor | Contract | Description | Ref. Date | Expiry | Source |
Aveng Moolmans
|
Mining
|
Moolmans was awarded the open cut contract by Tshipi é Ntle in October 2011. The initial five-year contract was a greenfields opportunity, with Moolmans establishing the entire open cut operation to provide a full mining service for overburden and manganese ore. Due to a downturn in the manganese price in 2016, the contract was reduced to 50 000 BCMs per month. The market has since recovered and Moolmans is once again providing a full mining service, which includes bush clearing, top soil stripping, drilling and blasting, loading and haul of ore and waste.
Aveng has announced that its South African based contract mining subsidiary, Moolmans, has entered into a new five-year contract with its long-standing client Tshipi é Ntle. The new contract is valued at approximately ZAR7 billion (over $400 million).
|
Jan 31, 2023
|
5
|
|
Eskom Holdings SOC Ltd
|
Power supply
|
Tshipi E Borwa Substation and 132 kV powerline.
|
Dec 28, 2022
|
|
|
Summary:
The Tshipi Mine is located on the southern extremity of the Kalahari Manganese Fields (“KMF”), which covers an area of approximately 23,000 hectares. The KMF is known to contain approximately 80% of the world’s in-situ manganese resources. It is important to note that the Tshipi orebody is contiguous with and is the direct extension of South32’s (formerly BHP) Mamatwan operation that has been producing manganese for over 50 years. The KMF is dominated by the Hotazel geological formation comprising three sedimentary manganese layers interbedded with banded iron formations. Of the three sedimentary manganese layers, the lower manganese deposit is the best developed and laterally continuous. The middle and upper manganese orebodies act as stratigraphic markers rather than potential mining targets given the relatively low manganese content contained in these layers.
The Hotazel Formation is underlain by basaltic lava of the Ongeluk Formation (Transvaal Supergroup) and directly overlain by dolomite of the Mooidraai Formation (Transvaal Supergroup).
The Transvaal Supergroup is overlain unconformably by the Olifantshoek Supergroup, which consists of arenaceous sediments, typically interbedded shale, quartzite and lavas overlain by coarser quartzite and shale. The different formations at the Tshipi Borwa Mine include the Mapedi and Lucknow units. The whole Supergroup has been deformed into a succession with an east-verging dip.
The Olifantshoek Supergroup is overlain by Dwyka Formation, which forms the basal part of the Karoo Supergroup. At the Tshipi Borwa Mine this consists of tillite (diamictite), which is covered by sands, claystone and calcrete of the Kalahari Group (SLR, 2017c).
Tshipi is exploiting the manganese from the banded iron stones of the Hotazel Formation. The ore is contained within a 30 to 45 m thick mineralised zone which occurs along the entire Tshipi Borwa Mine and is made up of three manganese rich zones; the Upper Manganese Ore Body (UMO), the Middle Manganese Ore Body (MMO) and the Lower Manganese Ore Body (LMO).
The lower manganese orebody (“LMO”) consists of banded, very fine-grained braunite-kutnahorite lutite, containing concretionary ovoids, laminae and lenticeles of Mn-calcite with which hausmanite is commonly associated. The LMO is 37.5 m thick on average, dips toward the north- west at an average of 7º, and is subdivided based on geological features and metal content, into six sub-zones termed “N, C, M, Z, Y, X”. The grouped N, C, and M zones average 19.5 m thickness, with 37.5% Mn grade and Mn/Fe ratio of 8.5. This constitutes the average grade ore mined by Tshipi. The overlying Z, Y and X zones contain 31.0% Mn and have a Mn/Fe ratio of 5. This constitutes Tshipi’s lowgrade ore that is either mined and blended with average grade ore, or sold as standalone low-grade product.
The poorly mineralised MMO is approximately 1 m thick and not economically viable.
The UMO is 10 cm to 15 cm thick and comprises moderate deposits of manganese.
Reserves at June 30, 2024
Mineral Resources are reported inclusive of Mineral Reserves.
Category | Tonnage | Commodity | Grade |
Proven
|
59,728,609 t
|
Manganese
|
35.84 %
|
Proven
|
59,728,609 t
|
Iron
|
4.9 %
|
Probable
|
22,511,386 t
|
Manganese
|
35.93 %
|
Probable
|
22,511,386 t
|
Iron
|
4.73 %
|
Proven & Probable
|
82,239,994 t
|
Manganese
|
35.86 %
|
Proven & Probable
|
82,239,994 t
|
Iron
|
4.85 %
|
Measured
|
120,759,778 t
|
Manganese
|
33.47 %
|
Measured
|
120,759,778 t
|
Iron
|
4.91 %
|
Indicated
|
74,236,381 t
|
Manganese
|
31.86 %
|
Indicated
|
74,236,381 t
|
Iron
|
4.85 %
|
Inferred
|
232,905,465 t
|
Manganese
|
32.44 %
|
Inferred
|
232,905,465 t
|
Iron
|
4.94 %
|
Total Resource
|
427,901,624 t
|
Manganese
|
32.63 %
|
Total Resource
|
427,901,624 t
|
Iron
|
4.92 %
|
Summary:
The Kalahari Manganese Field, which is 35km long and 15km wide, is the largest Mnbearing geological formation in the world. Tshipi Mine is an open pit Mn mine with an integrated ore processing plant. Tshipi Mine is located on the southwestern outer rim of the Kalahari Manganese Field, hence the ore resources are shallower and more amenable to open pit mining.
The Tshipi ore body commences at a depth of 70m below the surface and the ores are contained within a 30m-45m thick mineralised zone which runs along the entire Property. The ore layer dips gradually to the northwest at about 5 degrees. Tshipi’s strategy is to mine and process the lower 15m of the mineralised zone, commonly known as the bottom cut, as it bears higher-grade ores. A portion of the upper 15m mineralised zone, referred to as the top cut, is planned to be stockpiled for possible use later.
The Tshipi Mine is an open-pit mine that operates through drill-and-blast and load-and-haul mining techniques. At the start of the mining process, the topsoil is removed and stockpiled in a separate area for later use during the rehabilitation phase.
The various layers of the Kalahari formation are removed, followed by the harder banded ironstone, dolomite and manganese layers which are part of the Hotazel formation. Once exposed, the manganese ore is drilled, blasted and loaded onto a truck and hauled to the primary crusher which forms part of the processing facilities.
The mining of the open pit commenced in the south-east of the mining right area and is progressing in a northerly direction. The depth of the manganese seam at the start of mining was approximately 70 m below the surface and the deepest point will be approximately 330 m below surface.
Once the topsoil and some of the waste rock has been removed by dozing, the waste rock is drilled and blasted in benches until the economic ore horizon is exposed. Similarly drill and blast methods are used to break the ore with careful attention being paid to avoiding contamination of the ore with waste.
Blasting occurs only a few times a week i.e. not daily and only in daylight hours. Blasting does not take place on weekends under normal circumstances. Access to the open pit is by means of engineered ramps from either the high wall, low wall or end wall of the pit.
In the future, access to the underground workings will be by means of adits or portals excavated off the high wall on the ore-body horizon i.e. on the floor of the open pit.
Broken waste rock is loaded into mining dump-trucks by excavator and then hauled either to the worked out area of the pit or onto the surface WRDs where it is tipped and dozed into final position.
Broken ore is also loaded by excavator into mining dump-trucks and then hauled either directly to the ROM pad – adjacent to the mine tip and crusher or to various grade stockpile areas.
Heavy Mobile Equipment
HME Type | Model | Quantity | Status | Leased or Contractor | Ref. Date | Source |
Dozer
|
|
4
|
Required
|
|
Jan 31, 2023
|
|
Drill
|
|
6
|
Existing
|
|
Apr 18, 2019
|
|
Excavator
|
|
3
|
Existing
|
|
Apr 18, 2019
|
|
Excavator
|
Liebherr R 9150
|
2
|
Existing
|
|
Jan 31, 2023
|
|
Truck (haul)
|
|
51
|
Existing
|
|
Apr 18, 2019
|
|
Truck (haul)
|
Caterpillar 785D
|
16
|
Existing
|
|
Jan 31, 2023
|
|
Comminution
Crushers and Mills
Type | Model | Size | Power | Quantity |
Jaw crusher
|
|
|
|
1
|
Cone crusher
|
|
|
|
1
|
Summary:
The ROM stockpile feeds the processing plant which is designed to treat 3.3-3.6 mtonnes p.a. of Mn ores. These products are stockpiled before loading through a stateof-the-art load-out station onto railway trains or road trucks. Inland transportation of Mn products from the mine site is carried out by rail, and complemented by a combination of road and rail solutions to increase logistics capacity. Tshipi’s products are then exported through: a) the Port Elizabeth bulk terminal; b) the Port Elizabeth multi purpose terminal; or c) the Saldanha multi-purpose terminal.
Primary crushing and screening
ROM is delivered to the primary crushing and screening plant with mining dump trucks. The primary (jaw) crusher reduces the size of the run-of-mine ore to fractions manageable by the secondary crusher i.e.
Crushed ROM ore is conveyed to the crushed ore stockpile, adjacent to the secondary crushing and screening plant.
Dust suppression by means of water sprays is installed at the tip, the primary crusher, screens and conveyor transfer points.
Secondary crushing and screening
The secondary crushing and screening plant is used to size the ore according to product specifications. Crushed ROM ore is first screened and the >75mm ore reports to a cone crusher before reporting to a the <75mm stockpile. The <75mm ore is then reclaimed by conveyor and screened to produce two stockpiles; a 75mmm X 6mm lumpy product and a <6mm fines product. Dust allaying by water sprays at the crusher, screens and conveyor transfer points is done continuously while the plant is in operation. The water is either retained as surface moisture on the ore or evaporates, there is minimal if any run-off water.
Front end loaders and haul trucks are used to transfer the ore to the product stockpiles adjacent to the rail load-out facility. As trains arrive at the mine product ore is reclaimed and put into the wagons via a load-out silo. Road trucks are loaded with front-end-loaders form the same product stockpiles.
Thickener and tailings dam (not constructed or commissioned at this time)
Secondary screening fines waste (<1 mm) material is sent to the thickener plant via conveyor. Water removed from the secondary screening fines waste during the thickener process is re-used within the mining system as process water for dust suppression at the primary and secondary screening plants. The fines waste processed at the thickener is disposed as tailings.
Tertiary crushing and screening (not constructed or commissioned at this time)
The tertiary crushing and screening section (-40+6 mm material) is used to prepare the ore for sinter plant feed. High grade product is stockpiled at the tertiary product stockpile prior to being sent to the sinter plant. Manganese that is below the required grade from the tertiary crushing and screening plant is stockpiled at a low grade stockpile prior to being sent to the Dense Medium Separator (DMS) for further processing. Any fines material (-1 mm) produced at the tertiary crushing and screening plant are sent to the thickener for disposal to the tailings dam.
Sintering (not constructed or commissioned at this time)
In the sinter plant, ore is sintered by the application of heat, to agglomerate it and to increase the manganese content (by burning off the carbonaceous material). Raw materials are mixed with the manganese ore in a rotating mixing pan prior to agglomeration in a rotary drum. The agglomerated material is fed into the sinter furnace on a steel belt. The sinter furnace is a multi- compartment oven that is ignited with gas or heavy fuel oil. The front compartments are used for drying, ignition and sintering. The back compartments are for cooling. Gas emissions are scrubbed in cascade scrubbers to remove most of the particulates and pollutants. The dirty scrubber water is re-cycled in the thickener plant. Dust emissions are captured in bag filters and recycled into the sinter feed. The final product is stockpiled on the product stockpile prior to being loaded onto trains for sale to third parties.
Dense medium separation (not constructed or commissioned at this time)
Prior to the sintering stage, manganese ore that is below the saleable manganese grade is beneficiated using DMS, effectively upgrading the ore. Using density differential between manganese and waste; the material is sent to the sinter feed stockpile prior to being sent to the sinter plant while the waste is disposed onto the temporary discard dump.
Recoveries & Grades:
Commodity | Parameter | 2024 | 2023 | 2022 | 2021 | 2020 | 2019 | 2018 | 2017 | 2016 | 2015 |
Manganese
|
Head Grade, %
| 37 | 37 | 37 | 37 | 37 | 37 | 37 | 37 | 37 | 37 |
Pipelines and Water Supply
Type | Material | Diameter | Length | Description |
Water pipeline
|
Steel
|
100 mm
|
500 m
|
|
Summary:
Potable water
The water for the mine is sourced from the Sedibeng Vaal Gamagara Water Supply pipeline. This water is piped to the on-site reverse osmosis treatment plant prior to use within the mine for potable use.
Tshipi requires a maximum of 27 387 m3/month of water from the Sedibeng Vaal Gamagara Water Supply pipeline.
Process water
Process water is currently provided by a combination of water from the Sedibeng Vaal Gamagara Water Supply pipeline (when make-up water is required), dewatering from the open pit, the collection of storm water runoff and from planned water supply boreholes within the Mining Right area. Tshipi requires a total of 9 432 m3/month. When the tailings dam and sinter plant are in operation, the process water requirements will increase to 15 004 m3/month.
Water storage facilities
One steel water tank (1 500 m3) is located in the plant area for the storage and dispensing of process water. This tank receives water from the storm water dam and sewage plant, the pit dewatering and from the Vaal Gamagara Water Supply pipeline. In addition to this, provision has been made for a steel water tank (1 000 m3) for the mining and primary crushing section stores. Further to this, provision is also made for various other water tanks (1 000 m3 each) to store and dispense potable water.
Pipelines
A pipeline (100 mm diameter) connection to the Sedibeng Vaal-Gamagara pipeline supplies the mine with potable and process water. Secondary pipelines (250 mm to 300 mm diameter) transfer water within the mining areas. These pipelines are located within the approved surface use area and are routed to support the operations at the Tshipi Borwa Mine. Secondary pipelines will be installed to transfer water between the return water dam and processing plant area when the tailings dam is operational.
A pipeline connection to the Sedibeng Vaal-Gamagara reservoir is located approximately 500m east of
the Tshipi Borwa Mine.
Water and Wastewater Management
Tshipi has expanded its onsite catchment capacity in terms of water storage dams from 39,000m3 to 91,000m3 with the operationalisation of the new storm water dam. The new 52,000m3 storm water dam increases Tshipi’s capacity to capture water during the rainy season and cater for a 1-in 50-year flood event. Tshipi has experienced significant rainfall in the past four years, which have filled all dams to nearly full capacity.
The storm water dam is linked by water channels to manage the levels of both the dirty water dam and storm water dam to prevent any water spill and balance the 1-in 50-year flood.
Collected storm water which is the least polluted water is further used for dust suppression of roads in the processing plant easing up the use of fresh potable water from Sedibeng Water, the potable water service provider.
The increase in rainfall in the past four years has significantly increased the available water in the pit that can used to reduce the need for fresh potable water from Sedibeng Water. Priority is given to first use pit water and then storage dam water for production. Going forward, Tshipi will establish reduction targets for freshwater use per tonne.
In the Northern Cape of South Africa, water management in mining takes on an added layer of complexity and urgency. In response to these challenges, in 2023, Tshipi expanded its onsite catchment capacity in terms of water storage dams from 39,000m3 to 91,000m3 with the operationalisation of the latest stormwater dam.
The stormwater dam has 52,000m3 capacity which increased water capture capacity during the rainy season and caters for a 1:50 year flood event.
Commodity Production
Waste OP means Waste and low-grade ore.
Commodity | Units | 2024 | 2023 | 2022 | 2021 | 2020 | 2019 | 2018 | 2017 | 2016 | 2015 |
Manganese
|
Mt
| 3.5 | 3.3 | 3.7 | 3.4 | 3.4 | 3.4 | 3.6 | 2.3 | 1.4 | 2.4 |
All production numbers are expressed as lump & fines.
Operational metrics
Metrics | 2024 | 2023 | 2022 | 2021 | 2020 | 2019 | 2018 |
Ore tonnes mined
| 729,335 bcm | | | | | | |
Waste
| 12,630,570 bcm | | | | | | |
Total tonnes mined
| 13,359,905 bcm | 9,628,220 bcm | 13,156,150 bcm | 12,014,820 bcm | 12,357,691 bcm | 11,234,344 bcm | 10,578,010 bcm |
Annual production capacity
| | 3.6 Mt of manganese lump & fines | | | | | 3.6 Mt of manganese lump & fines |
Production Costs
| Commodity | Units | 2024 | 2023 | 2022 | 2021 | 2020 | 2019 | 2018 | 2017 |
Cash costs
|
Manganese
|
USD
|
2.21 / dmtu
|
2.03 / dmtu
|
1.93 / dmtu
|
2.05 / dmtu
|
2.14 / dmtu
|
2.27 / dmtu
|
2.09 / dmtu
|
2.2 / dmtu
|
Operating Costs
| Currency | 2018 |
OP mining costs ($/t mined)
|
USD
| 1.7 |
Mine Financials
| Units | 2024 | 2023 | 2022 | 2021 | 2020 | 2019 | 2018 | 2017 |
Revenue
|
M ZAR
| | 9,162 | 7,394 | 7,499 | 8,023 |
10,148
|
7,141
|
3,777
|
Operating Income
|
M ZAR
| | 2,742 | 1,387 | 2,302 | 2,933 |
5,441
|
3,098
|
1,331
|
Gross profit
|
M ZAR
| | 2,802 | 1,320 | 2,336 | 2,962 |
5,474
|
3,159
|
1,427
|
Pre-tax Income
|
M ZAR
| | 2,698 | 1,334 | 2,032 | 2,749 |
5,208
|
2,712
|
1,239
|
After-tax Income
|
M
| 81.5 AUD | 1,982 ZAR | 943.1 ZAR | 1,463 ZAR | 1,976 ZAR |
3,749 ZAR
|
1,902 ZAR
|
891 ZAR
|
EBITDA
|
M
| 119 AUD | 266 AUD | 139 AUD | 206 AUD | 314 AUD |
580 AUD
|
|
|
Personnel
Job Title | Name | Profile | Ref. Date |
Buyer
|
Fundi Mbudi
|
|
Dec 17, 2024
|
Chief Executive Officer
|
Ezekiel Lotlhare
|
|
Dec 17, 2024
|
Logistics Manager
|
Ntshantsha Miggels
|
|
Dec 17, 2024
|
Managing Director and CEO
|
Brad Rogers
|
|
Dec 17, 2024
|
Mining Manager
|
Maryna Madelein Smith
|
|
Dec 17, 2024
|
Procurement Superintendent
|
Buyiswa Modibedi
|
|
Dec 17, 2024
|