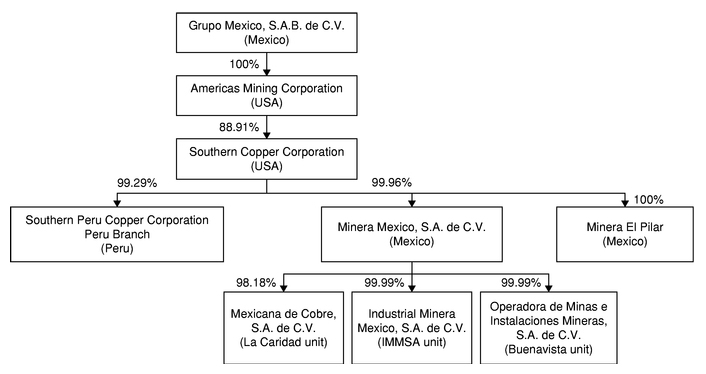
Southern Copper Corporation (SCC) is an indirect subsidiary of Grupo Mexico S.A.B. de C.V. (Grupo Mexico) which owns 88.91% of SCC through its wholly-owned subsidiary Americas Mining Corporation (AMC).
SCC’s operations in Mexico are conducted through its subsidiary, Minera Mexico, S.A. de C.V. (Minera Mexico). SCC owns 99.96% of Minera Mexico.
Operadora de Minas e Instalaciones Mineras, S.A de C.V. (the “Buenavista unit”) operates Buenavista, an open-pit copper mine.
Contractor | Contract | Description | Ref. Date | Source |
Comision Federal de Electricidad (CFE)
|
Power supply
|
A minor portion of the site demand is supplied by Comisión Federal de Electricidad (CFE), the state’s electrical power producer.
|
Feb 11, 2025
|
|
Mexico Generadora de Energia S. de R. L.
|
Power supply
|
The bulk of the demand is supplied by MGE, a subsidiary of Grupo Mexico, the majority stockholder of Southern Copper. MGE owns and operates a power generation plant consisting of two trains.
|
Feb 11, 2025
|
|
Deposit type
- Porphyry
- Vein / narrow vein
- Breccia pipe / Stockwork
Summary:
The Buenavista del Cobre deposit in the Cananea mining district is divided into two target zones, namely Buenavista Copper (BVC) and Buenavista Zinc (BVZ). The BVZ deposit conformably underlies the BVC deposit and is located to the northwest of the BVC deposit.
The Buenavista del Cobre mine is Mexico's largest porphyry Cu deposit. Cu mineralization in the Cananea mining district centers around quartz monzonite intrusions and breccia chimneys. Main production focuses on high-grade brecciated bodies, such as La Colorada Breccia, which hosts significant Cu, Au, and Ag mineralization.
Other important breccias include El Capote, Oversight Cananea-Duluth, La Demócrata, El Kirk, Henrietta, América Bonanza, and Veta 5. These structures are related to vertical, circular or oval intrusive trunk domes extending hundreds of meters deep, with angular or semi-rounded rock fragments in a matrix of massive sulfides and quartz.
Northwest of the BVC deposit is the BVZ deposit, a skarn type poly-metallic deposit containing Zn, Cu, and Ag. Carbonate rocks of the Capote Basin and Puertecitos show alteration and mineralization from multiple events of intrusion of granites and quartz monzonitic porphyries. The skarn deposits at Puertecitos and the Elisa mine are related to favorable replacements in mantles. In contrast, the Capote Basin ore bodies occur in zones with pyrite and silica associated with brecciated chimneys.
The predominant mineralization at Puertecitos and Elisa consists of bornite and chalcopyrite with minor sphalerite. Secondary Cu enrichment occurred locally. In the Capote Basin, mineralization is associated with silicified zones with pyrite and calcite. The hypogene ore sulfides are chalcopyrite, sphalerite, and locally, chalcocite.
Mineralization
Much of the Cu mineralization in the Cananea mining district is found in disseminated form and in veinlets in stockwork zones in the volcanic and intrusive rocks. Higher Cu grades are hosted in breccia structures, contact zones and some replacement bodies. Supergene enrichment constitutes important zones of Cu mineralization, formed by chalcocite - covellite - digenite, generally replacing pre-existing primary minerals (pyrite - chalcopyrite).
The distribution of mineralization in this zone is in disseminated form associated with volcanic rocks and porphyries of quartz-monzonite composition; in the replacement zone the occurrence of mineralization is in disseminated, nodular (patchy) form by cavity filling and replacement along the bedding planes. Underlying the supergene enrichment is a primary mineralization composed predominantly of chalcopyrite, with a minor amount of bornite. The distribution of mineralization is predominantly in veinlets, in disseminated form occurring in very fine grains with abundant occurrence of chalcopyrite-based copper minerals.
A layer of hematite - goethite - jarosite oxides is found above the supergene enrichment between elevations 2,200m to 1,800 m. The presence of native limonite suggests early enrichment cycles. The chalcocite-based supergene enrichment zone lies between elevations 1,800 m to 1,650 m amsl.
The zone of supergene chalcocite and hypogene chalcopyrite mixed sulfides is between elevations 1,650 m to 1,400 m amsl. The occurrence of mineralization in the mixed zone is in two forms: disseminated and veinlets. At greater depths, disseminated mineralization diminishes while veinlet mineralization becomes more prevalent. In this zone, chalcocite and chalcopyrite coexist.
Hypogenic primary chalcopyrite mineralization occurs below elevation 1,400 m and is known up to an elevation of400 m amsl. Iron oxides and supergene minerals are often found in fault 8-125 at depths over 300 meters.
The Capote basin hosts most of the important skarn mineralization (Meinert, 1980). Additional skarn mineralization is found in the Elisa and Puertecitos mining areas. Both prograde and retrograde skarns are present, but only retrograde skarns contain economic quantities of Cu and Zn minerals.
Reserves at December 31, 2024
Mineral reserves are reported on an elevated cut-off grade for the first three years of the mine schedule and then on a break-even plant and leach profit basis for the remaining LOM schedule. The estimate was based on the long- range schedule, inclusive of processing costs and transport streams and based on a Cu price of $3.30/lb, Mo price of $10.00/lb and Zn price of $1.15/lb. Mineral reserves are reported using a cut-off grade optimization strategy with elevated copper feed grade targets of 0.50% (2025), 0.48% (2026), 0.43% (2027) and 0.40% (2028+) based on a long-range schedule.
Mineral Resources Cut-off grade: mineral resources are reported on break-even plant and leach profit basis. The estimate was constrained to the Resource pit based on a Cu price of $3.795/lb, Mo price of $11.50/lb and Zn price of $1.323/lb.
Category | Ore Type | Tonnage | Commodity | Grade | Contained Metal |
Probable
|
ROM leach
|
2,118 Mt
|
Copper
|
0.27 %
|
12,389 M lbs
|
Probable
|
Sulphide
|
2,413 Mt
|
Copper
|
0.44 %
|
23,307 M lbs
|
Probable
|
Sulphide
|
2,117 Mt
|
Molybdenum
|
0.009 %
|
399 M lbs
|
Probable
|
Sulphide
|
296 Mt
|
Zinc
|
0.58 %
|
3,758 M lbs
|
Indicated
|
ROM leach
|
53 Mt
|
Copper
|
0.33 %
|
377 M lbs
|
Indicated
|
Sulphide
|
830 Mt
|
Copper
|
0.39 %
|
7,228 M lbs
|
Indicated
|
Sulphide
|
830 Mt
|
Molybdenum
|
0.007 %
|
129 M lbs
|
Indicated
|
Sulphide
|
830 Mt
|
Zinc
|
0.12 %
|
2,199 M lbs
|
Inferred
|
ROM leach
|
373 Mt
|
Copper
|
0.18 %
|
1,457 M lbs
|
Inferred
|
Sulphide
|
8,553 Mt
|
Copper
|
0.34 %
|
64,287 M lbs
|
Inferred
|
Sulphide
|
8,553 Mt
|
Molybdenum
|
0.008 %
|
1,524 M lbs
|
Inferred
|
Sulphide
|
8,553 Mt
|
Zinc
|
0.05 %
|
9,605 M lbs
|
Summary:
The ore at Buenavista del Cobre is recovered using open-pit conventional truck and shovel bulk mining methods with in-pit crusher conveyor systems due to the proximity of the ore to the surface and the physical characteristics of the deposit. Mining operations mine the deposit in phases to minimize strip ratio in any given year and to maximize the amount of ore being fed to the concentrators. The majority of the ore is hauled to one of the in-pit crushers and conveyed to either Concentrator I or II, or to the leach pads. Likewise, most of the waste is currently hauled to overburden storage facilities (OSF).
Drill and Blast
Buenavista del Cobre uses a fleet of 14 production drills; all of the drills are large diameter capable of drilling 12 ¼“ blast holes. The drills are a combination of CAT 6380 and PIT VIPER 351 drills. Blasting at Buenavista del Cobre is conducted with ANFO and emulsion depending on the condition of the patterns. For instance, overburden blasts are typically conducted with ANFO while patterns in areas of the pit effected by water are completed with emulsion.
Pit Slope Design Recommendations
The slope design for Buenavista Copper is provided for four design zones.
The mine design criteria are listed below:
- Bulk open pit truck and shovel mining with in-pit crushing conveying
- Minimum operating bench width of 65 m
- Haul road design width of 65 m (assumes blasted ramp, running surface width 30 m – 40 m)
- Bench height of 15 m (double benching, 30 m total bench height)
- Maximum road grade of 8% Bench face angle of 65°
- Typical blasting bench height 15 m
- Average specific gravity of 2.6
- Berm width and slope angle varies based on geotechnical sector
Mining Strategy and Production Rates
The mine plan targets 74 Mtpa of combined ore to Concentrator I and II. PR1 and Concentrator I are decommissioned in 2036 due to start of mining at Zinc1 phase thus reducing the capacity to 43 Mtpa thereafter.
Design Phases
The strategy for the phase design was to be able to blend the materials such that a blended copper concentrate with zinc grade less than 0.1% can be sent to the copper concentrators. Also, the phases delineated the zinc rich phases such that the very high grade material from the zinc phases which could not be blended could be transported to the primary crushers for processing at the zinc plant.
This above strategy led to the development of one south phase, two phases on the western side, two phases on the norther side and four zinc phases on the eastern side. These phases were mined at various rates with the goal of blending the material as well as achieving higher grades to the copper concentrators.
Production Schedule
The production schedule was a blended schedule that with the strategy of maximizing the ore to the copper and zinc concentrators while performing cut off grade optimization by raising the mill feed grade The goal was to also simultaneously send a copper blend with average zinc grade below 0.1% to the copper concentrator. The targets were 74 MT of total ore to the two concentrators till Concentrator I was mined out in Year 12. This reduced the overall copper ore feed to 43 Mt (Concentrator II) for the rest of the mine life. The Zinc Concentrator could process 7.3 Mt for the life of mine.
The strategy also included sending a higher grade of 0.5% Cu to the copper mills with a declining grade profile till 0.4% for the first 5 years. The overall grade was targeted at 0.4% to the copper concentrators for the life of mine. Similarly, a zinc grade of 1.2% was targeted for the zinc plant for the first 11 years following which the zinc plant was transformed into a copper cleaner plant which could float out the higher zinc grades as a zinc concentrate allowing for a cleaner copper concentrate. Mining was limited to 8-10 vertical benches per year with a maximum of 2 open benches per phase. The total material movement that the mine could move was 365 Mt per year.
BVC production schedule is contingent on the following major infrastructure moves which allow access to the different phases at different times in the mine schedule. These include:
1. Demolition of PR1 and PR3: PR1 and PR3 are demolished in Year 12 to allow access to the Zinc 1 phase.
2. Installation of PR5: PR5 is installed at the north-east part of the pit to replace PR3. Post decommissioning of PR3, PR5 supplies ore with high grade zinc to the Zinc plant. PR5 needs to be commissioned before the start of Year 12. This would allow for a continuous feed to the Zinc plant.
3. Moving the west belt: The west belt is moved towards west by Year 14. This allows access to the West 2 phase underneath.
4. Demolition of Concentrator 1 and Zinc Plant: The Concentrator 1 and Zinc Plant are demolished by Year 18 to allow access to the Zinc 3 phase.
5. Installation of new Zinc Plant: A new zinc plant is established close to the PR5 primary crusher by Year 18 that takes in the ore with higher grade zinc. This installation needs to be matched up with the decommissioning of the old zinc plant to allow for continuous processing of the zinc ore.
Equipment
The mine uses a combination of CAT, Komatsu, P&H and Bucyrus equipment for material extraction and transportation. Currently, the largest haul truck on site is the CAT 797F and Komatsu 980-E with a capacity of 360 t; additional trucks include the Komatsu 830E (210 t), the Komatsu 930E (275 t), and the Komatsu 960E (327 t). The shovels used at the site are mainly electric rope shovels, ranging from the P&H 2800 XPA with a 28 m3 capacity up to the P&H 4100 XPC with a 57 m3 capacity.
The excavator fleet size averages 10 units during the LOM decreasing along with the tonnage mined. About 15 equivalent shovels are required in Year 1 decreasing to 8 in 2045 and onward. During the early years, old electric rope shovels P&H 2800 and Bucyrus-Erie 495 BI will be decommissioned and substituted by P&H 4100.
The haul truck fleet size averages 143 units over the LOM. The support equipment fleet includes front end loaders, production drills, track and wheel dozers, motor graders, cable trucks, and water trucks.
Heavy Mobile Equipment
HME Type | Model | Size |
Drill - EV
|
Bucyrus-Erie 49RIII
|
|
Drill - EV
|
Bucyrus-Erie 49HR
|
|
Drill - EV
|
Epiroc PV-351
|
|
Drill - EV
|
Caterpillar MD6380
|
|
Loader (FEL)
|
Komatsu WA1200
|
|
Loader (FEL)
|
Komatsu WA900
|
|
Loader (FEL)
|
Komatsu WA900
|
|
Loader (FEL)
|
Komatsu WA450
|
|
Loader (FEL)
|
Caterpillar 924G
|
|
Shovel (rope) - EV
|
P&H 2800 XPB
|
|
Shovel (rope) - EV
|
P&H 2800XPA
|
28 m3
|
Shovel (rope) - EV
|
P&H 4100 XPA
|
|
Shovel (rope) - EV
|
P&H 4100 XPC
|
57 m3
|
Truck (haul)
|
Komatsu 980E
|
360 t
|
Truck (haul)
|
Terex MT4400
|
|
Truck (haul)
|
Caterpillar 797F
|
360 t
|
Truck (haul)
|
Komatsu 830E
|
210 t
|
Truck (haul)
|
Komatsu 930E
|
275 t
|
Truck (haul)
|
Komatsu 960E
|
327 t
|
EV - Electric
Comminution
Crushers and Mills
Type | Model | Size | Power | Quantity |
Gyratory crusher
|
|
54" x 69"
|
|
1
|
Gyratory crusher
|
|
60" x 89"
|
|
4
|
Cone crusher
|
Metso Nordberg MP1000
|
|
|
18
|
Cone crusher
|
Metso Nordberg HP4
|
|
|
1
|
SAG mill
|
|
30' x 15.5'
|
|
1
|
Ball mill
|
|
23' x 37'
|
|
1
|
Summary:
Buenavista Copper (BVC)
BVC Dry Process Crushing and Screening
The simplified process flowsheets for the crushing and screening plants are provided below:
- The run-of mine material is transported to the primary crushers with haul trucks. The haul trucks discharge directly into the crushers.
- Size reduction of the ROM ore is accomplished by two primary 60 x 89 gyratory crusher to 80% passing minus 200 mm (85% - 6”). The primary crushed ore is stored in a covered coarse ore stockpile and then reclaimed by apron feeders and a conveyor belt.
- The primary crushers for Concentrator I are located on the east side of the existing pit limit, near the concentrator. These crushers process 4,670 dtph, 84,000 dry tpd (75% availability, 18 hours of operation) with 6-inch closed size setting (P80 minus 152 mm). The primary crushed material is conveyed to a covered coarse ore stockpile.
- The primary crushers for Concentrator II are located on the north-west side of the pit and the ore is transported 5.4 km by conveyor belts to the coarse ore stockpile near Concentrator II. These crushers process 5,560 dtph, 100,000 dry tpd (75% availability, 18 hours of operation) with 6-inch closed size setting (P80 -152 mm).
- The coarse ore stockpiles provide one day of surge capacity to protect the downstream circuits from any eventualities in the primary crushers, or the mine.
- The crushing circuit design includes weigh scales, crushed ore sampling system and magnetic separators to protect the equipment from iron debris coming from the mine.
- Size reduction of the ore is by secondary and tertiary crushing and screening. The secondary and tertiary crushers operate in closed circuit with tertiary screens to reduce the ore size from 200 mm to 80% -8-12 mm(96% - ½”).
- Crushed ore is conveyed to the fine ore stockpile buildings.
- When full, the fine ore storage provides one day of surge capacity to protect the beneficiation circuits from any eventualities in the crushing/screening circuit.
- Fine crushed ore is reclaimed and conveyed to the grinding circuits.
BVC Wet Process Beneficiation Plant Grinding
The simplified process flowsheets for the grinding is provided below:
- The beneficiation plant will operate at an estimated 90.0% availability.
- Ore grinding is achieved in conventional ball mill circuits operating in parallel prior to processing in flotation circuits. Concentrator I has 5 grinding circuits with two 16.5-ft diameter by 27-ft long ball mills per section. Concentrator II has six grinding circuits, with a single 24-ft diameter by 42.5-ft long ball mill. The ball mills operate in closed circuit with hydro-cyclones to deliver an ore size of 80% passing 105 µ to the flotation circuit.
Buenavista Zinc (BVZ)
- The process operations required to extract zinc and copper from the BVZ sulfide ores are summarized below. The concentrator follows a conventional process of crushing, screening, semi-autogenous grinding (SAG), ball milling, and sequential flotation to separate zinc and copper concentrates.
- Size reduction of the ROM ore is crushed in an existing primary gyratory crusher to 80% passing -121 mm. The primary crushed ore is stored in a covered coarse ore stockpile and then reclaimed by apron feeders and a conveyor belt.
- Ore comminution follows in a SAG mill to reduce the ore size from approximately 80% passing -121 mm to a size of approximately 80% passing 1.9 mm prior to pumping to a ball mill for grinding. The SAG mill operates in closed circuit with a vibrating screen and pebble crusher.
- Ore grinding is achieved in a conventional ball mill operating in closed circuit with hydro-cyclones, to deliver a product size of 80 percent passing 119 microns to the flotation circuit.
BVZ Primary Crushing & Grinding
A brief description of the crushing and grinding circuits included in the design is provided below:
1) Crushing (single stage circuit):
- Primary Crushing. Existing 54” x 69” gyratory crusher.
- Ore conveyor to Coarse ore stockpile.
- Coarse ore storage yard. 80,000 tonnes total capacity; 20,000 dry tonnes live capacity.
- Reclaim Apron Feeders & Conveyors. Six sets.
2) Grinding:
- SAG mill [30 ft x 15.5 ft (9.14 m x 4.85 m) operated in closed circuit with vibrating screen and pebble crusher]
- Pebble crusher – Open circuit (Short head cone – Metso HP4)
- Ball Mill operating in closed circuit with hydro-cyclones. [23 ft x 37 ft (7 m x 11 m)]
Processing
- Sulfuric acid (reagent)
- Crush & Screen plant
- Flotation
- ROM/dump leach
- Dewatering
- Filter press
- Solvent Extraction & Electrowinning
Summary:
Material is mined, transported, and crushed for processing to recover copper concentrate, molybdenum concentrate, and zinc concentrate. Two copper beneficiation plants (BVC), Concentrator I and Concentrator II, are in operation at Buenavista del Cobre. Concentrator I has been in operation since 1986 and Concentrator II since 2016. The two concentrators follow a conventional process of crushing, screening, ball milling and sequential flotation to separate copper and molybdenum concentrates. The differences between the two plants are size of the equipment and the number of machines dedicated to each unit operation, because Concentrator II was designed and built with modern equipment 30 years after Concentrator I.
Zinc and copper extracted from the Buenavista del Cobre sulfide ores with higher zinc content will be sent to the Zinc concentrator or one of the Cu concentrators if the average zinc grade can be blended to be less than 0.1%.
The Zinc plant (BVZ) extracts the zinc concentrate from the feed which is then sent to a copper flotation unit (part of the Zinc plant) to extract copper. The resulting copper is a clean copper with zinc grade below 0.1%. During the initial 11 years, the Zinc plant is fed with target head grade material of 1.2% zinc to realize the zinc concentrate. From Year 12, the plant acts as a copper “cleaner” unit with high grade zinc concentrations removed as a zinc concentrate while the plant provides high grade clean copper (with zinc below 0.1%) as the principal output. The copper concentrate slurry is sent to the thickening section of the existing Concentrator I.
Buenavista del Cobre processing facilities also include three leaching, solvent extraction and electrowinning (LSX-EW) plants. The leachate facilities identified as Quebalix I to IV are located adjacent to leach pads. The leach pad at each Quebalix facility is fed with leachable ore that is crushed, transported, and stacked with belt conveyors. The primary process for Buenavista del Cobre is conventional milling/flotation of ore targeting a headgrade of 0.5% total copper, however the mine is in the process of lowering the target grade to 0.4% total copper over the next few years. The L-SX-EW process is used to produce pure copper cathode.
Buenavista Copper
The BVC facilities include:
- Two beneficiation plants: Concentrators I and II.
- Three Solvent Extraction and Electrowinning plants (SX-EW – I to III).
- Leaching: Three ROM leach areas and four crushed ore leach areas (Quebalix I to IV). The Quebalix I leach area has been deactivated and the crusher is operating to feed ore to the Zinc Concentrator.
BVC Wet Process Beneficiation Plant Flotation Circuits, Equipment, and Process Description
- The flotation circuit design provides for selective recovery of copper and molybdenum mineralization. The flotation plants consist of copper-moly bulk flotation, copper-moly separation, moly and copper cleaner flotation circuits. In Concentrator I, the bulk flotation circuit consists of 90 flotation cells, with each cell having a capacity of 1,000 cubic feet (ft3 ). In Concentrator II, the bulk flotation circuit consists of four rows of rougher flotation and four rows of first cleaner/scavenger cells and one row of second cleaner flotation. Each rougher row consists of seven 300 m3 tank type flotation cells. The copper flotation circuit includes regrind in a ball mill.
- Final tails from moly separation circuit are the copper concentrate. This is sent to a thickener, then a filter and stockpile to be loaded in truck/railroad for shipment to a subsidiary smelter or to port for export to market.
- Final molybdenite concentrate is thickened, filtered, dried, and packaged into bulk-bags for shipment to market.
- Rougher flotation tailings are thickened and deposited in TSF areas near the mine site, 5 km to the east from Concentrator I and 8 km to south for Concentrator II.
BVC Solvent Extraction and Electrowinning Process Description
The purpose of the SX plant is to concentrate Cu from a dilute impure pregnant leach solution (PLS) and produce a clean electrolyte at 45 to 55 g Cu/L suitable for the EW process. The main impurities deleterious to EW to be rejected in SX are iron and manganese. This is accomplished by selectively extracting Cu from the aqueous PLS into an organic solution, which consists of a Cu extractant reagent diluted in purified kerosene.
The SX plants have extraction sections and stripping sections that together form a “train”. A plant can have multiple trains and multiple stages in a section. Sometimes an organic washing stage is included. A stage consists of mixing tanks and a settler area to separate the solutions.
In the extraction section, the PLS is mixed with an organic solution, a mixture of a reagent diluted with kerosene, that extracts (loads) the copper from solution and releases acid. The mixture passes from the mixers to the settler where is separated into an aqueous solution and the loaded organic (LO) solution. The aqueous solution depleted of copper (Raffinate) returns to Leaching, to extract more copper and the organic solution advances to the Stripping section.
In the Stripping section, the LO is mixed with a highly acidic solution, called spent or lean electrolyte (SE). The high acid content of the SE causes the LO to release copper to the SE and pick-up acid, regenerating the reagent molecules and the SE becomes Rich Electrolyte (RE) to feed the EW plant. After separation of the phases in the settlers, the organic solution (SO) depleted of copper returns to extraction to load more copper and the electrolyte advances to EW to deposit copper as cathode in the EW cells.
In EW, the RE from SX is recirculated through electrowinning cells with multiple stainless-steel cathodes and lead anodes. A direct electrical current is applied to the cells that causes the copper in the RE to be deposited in the cathodes and the RE becomes SE that returns to SX to extract more copper.
Buenavista Zinc (BVZ)
The process operations required to extract zinc and copper from the BVZ sulfide ores are summarized below.
- The copper flotation circuit consists of two stages of rougher flotation, rougher scavenger flotation and two stages of cleaner flotation. Rougher scavenger concentrate is reground and returned to the second stage of copper rougher flotation. The zinc flotation circuit consists of two stages of rougher flotation, rougher scavenger flotation and three stages of cleaner flotation.
- The copper rougher scavenger flotation concentrate regrind circuit consists of a vertical grinding mill operated in open circuit with hydro-cyclones, to deliver a scavenger concentrate size of 80 percent passing 25 microns to the copper rougher flotation second stage.
- Final copper concentrate is directed to an existing copper concentrate thickener at BVC’s Concentrator I.
- The final zinc concentrate product is dewatered and filtered prior to loading in trucks for shipment. Water from the dewatering operation will be directed to a dedicated process water tank for reuse at the zinc concentrator.
- The zinc rougher scavenger flotation tails (final tailings) flows by gravity to a zinc tailings thickener. Thickener underflow is discharged by gravity to the existing Copper Concentrator I TSF for final disposal.
- Thickener overflows from tailing and concentrate sedimentation will be pumped to the process reclaimed water tank for reuse in the process.
- Plant water streams include process water, freshwater, pump seal water and domestic water. Freshwater from the south pond at Concentrator I is used for plant services, reagent mixing, and as gland seal water.
- Storing, preparing, and distributing reagents used in the process. Reagents include milk of lime, complex ZZ, A-3739 collector, zinc sulfate, copper sulfate, A-3473 collector, Teuton 100-35 frother, DP-6, flocculant and antiscalant.
Recoveries & Grades:
Commodity | Parameter | 2024 | 2023 | 2022 | 2021 | 2020 | 2019 | 2018 | 2017 | 2016 | 2015 |
Copper
|
Concentrate Grade, %
| 22.5 | 22.6 | 22.9 | 23.3 | 23.9 | 23.8 | 23.7 | 23.4 | 23.8 | 23 |
Molybdenum
|
Recovery Rate, %
| 71.6 | 70.8 | 70.5 | 69 | 67.3 | 65.6 | 58.4 | 39.9 | 25.1 | 25.6 |
Molybdenum
|
Head Grade, %
| 0.011 | 0.011 | 0.01 | 0.01 | 0.011 | 0.013 | 0.012 | 0.013 | 0.013 | 0.013 |
Molybdenum
|
Concentrate Grade, %
| 51.6 | 51.6 | 51.2 | 51.2 | 52.4 | 51.8 | 51.1 | 51.4 | 49.5 | 50.3 |
Zinc
|
Recovery Rate, %
| 81.1 | | | | | | | | | |
Zinc
|
Head Grade, %
| 2.15 | | | | | | | | | |
Zinc
|
Concentrate Grade, %
| 48.2 | | | | | | | | | |
Copper
|
Recovery Rate, %
| | | | | | | | | 70.8 | 47.8 |
Summary:
The site has a concession from the Comisión Nacional del Agua (the National Water Commission or the “CNA”) to pump water from wells drilled around the Cananea area against a fee. The wells pump approximately 35 Mm3 annually and are connected to a distribution piping network that feeds water to different consumers The site has plans in place for freshwater conservation by reducing the consumption and recycling for reuse when possible. About 78% of the site’s demand for water was reportedly covered by recycled water in 2023 and 2024, respectively.
Buenavista Copper
The water system for BVC is comprised of two separate systems:
- Freshwater.
- Reclaimed Water.
Freshwater is supplied from a 48-well field located approximately 10 km north-east of the mine, over two separate aquifers. Pumping from the wells is rotated, to maintain a proper level in the aquifers.
In 2023, the freshwater make-up requirement for Concentrator II was 1,994 m3 /h equivalent to approximately 0.4tonnes of freshwater per tonne of ore processed. The process water (reclaimed) is estimated at 7,140 m3/h, of which 2,250 m3 /h are recovered from the New Tailings Storage Facility (TSF No. 3).
In 2023, Concentrator I received 1,650 m3 /h of freshwater and 4,980 m3 /h from TSF No. 2.
Freshwater is pumped to a regulating reservoir, then to the south pond at Concentrator I from where it is distributed to the process areas, including the potable water and the fire water systems.
Reclaimed water is returned from the Tailings Thickeners, concentrate thickeners, and Tailings Dams.
Water reclaimed from the plant thickeners is discharged to a process water pond, then it is pumped to the process water head pond. Water from the tailings dam is also pumped to the process water head pond. The process water head pond distributes water by means of pumps to maintain proper pressure throughout the following processing circuits:
- Grinding Classification (dilution water)
- Flotation (launder water).
- Lime plant.
Reportedly, the leaching operations have suffered a shortage of water, due to lower-than-normal rains. BVC is acquiring new water rights and is working on expanding the raw water supply.
Buenavista Zinc
The water system for BVZ is comprised of two separate systems:
- Freshwater.
- Reclaimed Water.
The freshwater make-up requirement for grinding/flotation is estimated at 10,338 m3 per day equivalent to approximately 0.5 tonnes of freshwater per tonne of ore processed. The process water (reclaimed) is estimated at 72,857 m3 per day.
Freshwater from the south pond at Concentrator I is pumped to a freshwater reservoir and distributed without further treatment to the following process areas:
- Make-up to reclaimed water.
- Process make-up water.
- Potable water.
- Pump’s gland water seals.
- Reagent mixing.
Reclaimed water is returned from the Zinc Concentrate Thickener and the Tailings Thickener. Water reclaimed from the plant thickeners is pumped to a reclaimed water reservoir The reclaimed water reservoir distributes water by means of pumps to maintain proper pressure throughout the following processing circuits:
- Grinding.
- Classification (dilution water).
- Flotation (launder water).
Currently, freshwater for the BVC existing operations is supplied from a 48-well field located approximately 10 km north-east of the mine, over two separate aquifers. Pumping from the wells is rotated to maintain a proper level in the aquifers. Reportedly, BVC is acquiring new water permits and developing new freshwater sources. The capital cost estimate for the BVZ project includes US$3.7 M for a freshwater aqueduct and distribution system.
Commodity Production
Since 2019 stripping ratio obtained dividing waste by leachable material plus ore mined.
Commodity | Product | Units | 2024 | 2023 | 2022 | 2021 | 2020 | 2019 | 2018 | 2017 | 2016 | 2015 |
Copper
|
Cathode
|
kt
| 84 | 88 | 93 | 82 | 98 | 100 | 89 | 112 | 131 | 122 |
Copper
|
Metal in concentrate
|
kt
| 349 | 329 | 339 | 341 | 334 | 338 | 325 | 319 | 316 | 162 |
Copper
|
Concentrate
|
kt
| 1,554 | 1,456 | 1,482 | 1,465 | 1,398 | 1,420 | 1,371 | 1,362 | 1,330 | 705 |
Molybdenum
|
Metal in concentrate
|
kt
| 5.9 | 5.4 | 5.4 | 5.2 | 5.5 | 6.1 | 8.4 | 3.5 | 1.6 | 0.9 |
Molybdenum
|
Concentrate
|
kt
| 11 | 10 | 10 | 10 | 10 | 12 | 9.6 | 6.7 | 3.2 | 1.9 |
Silver
|
Metal in concentrate
|
koz
| 6,304 | 4,669 | 5,208 | 4,774 | 5,550 | 5,755 | 5,162 | 4,988 | 4,819 | 2,367 |
Zinc
|
Metal in concentrate
|
kt
| 64 | | | | | | | | | |
Zinc
|
Concentrate
|
kt
| 133 | | | | | | | | | |
Operational metrics
Metrics | 2024 | 2023 | 2022 | 2021 | 2020 | 2019 | 2018 | 2017 | 2016 | 2015 |
Daily processing capacity
| 197,000 t of ore (in concentrator) | 197,000 t of ore (in concentrator) | 197,000 t of ore (in concentrator) | 197,000 t of ore (in concentrator) | 182,000 t of ore (in concentrator) | 182,000 t of ore (in concentrator) | 176,700 t of ore (in concentrator) | | | |
Annual production capacity
| 174,470 t of copper cathode | 174,470 t of copper cathode | 174,470 t of copper cathode | 174,470 t of copper cathode | 174,470 t of copper cathode | 174,470 t of copper cathode | 174,470 t of copper cathode | | | |
Stripping ratio
| 0.64 | 0.66 | 0.72 | 0.52 | 0.29 | 0.37 | 3.23 | 3.14 | 2.88 | 6.23 |
Ore tonnes mined
| 204,054 kt | 194,020 kt | 196,810 kt | 213,304 kt | 201,013 kt | 211,419 kt | 215,717 kt | 227,575 kt | 190,066 kt | 184,272 kt |
Total tonnes mined
| 335,904 kt | 322,142 kt | 337,727 kt | 324,860 kt | 259,860 kt | 288,882 kt | 297,718 kt | 288,716 kt | 257,395 kt | 282,954 kt |
Tonnes processed
| 77,493 kt of ore (in concentrator) | 72,609 kt of ore (in concentrator) | 74,121 kt of ore (in concentrator) | 74,302 kt of ore (in concentrator) | 73,011 kt of ore (in concentrator) | 70,371 kt of ore (in concentrator) | 70,328 kt of ore (in concentrator) | | | |
Production Costs
Commodity production costs have not been reported.
Mine Financials
| Units | 2024 | 2023 | 2022 | 2021 | 2020 | 2019 | 2018 | 2017 |
Book Value
|
M USD
| 3,115 | 3,228 | 3,070 | 3,260 | 3,304 |
3,298
|
3,431
|
3,592
|
Personnel
Job Title | Name | Profile | Ref. Date |
Maintenance Superintendent
|
Alejandro Marquez
|
|
Aug 26, 2025
|
Maintenance Superintendent
|
David García
|
|
Aug 26, 2025
|
Mine Manager
|
Christian Torrecillas
|
|
Aug 26, 2025
|